Limak İnşaat Röportajı
Avrupa’nın en büyük, dünyanın ise 3. büyük barajı olan ’Yusufeli Barajı ve Hidroelektrik Santrali Projesi’ inşaatı Limak Holding taahhüdüne devam ederken, Şantiye Şefi Bülent Çakır ile proje hakkında görüştük.
Bülent Bey, öncelikle kısaca kendinizden bahseder misiniz?
Yaklaşık olarak sekiz senedir Limak Holding’de çalışmaktayım. Eylül 2013’en beri de Yusufeli Barajı’nda şantiye şefi olarak görev yapmaktayım. Daha önce yine Limak Holding’e ait İzmir’de Burgaz Barajı, Aydın’da Karacasu ve İkizdere Barajı Projelerinde görev aldım.
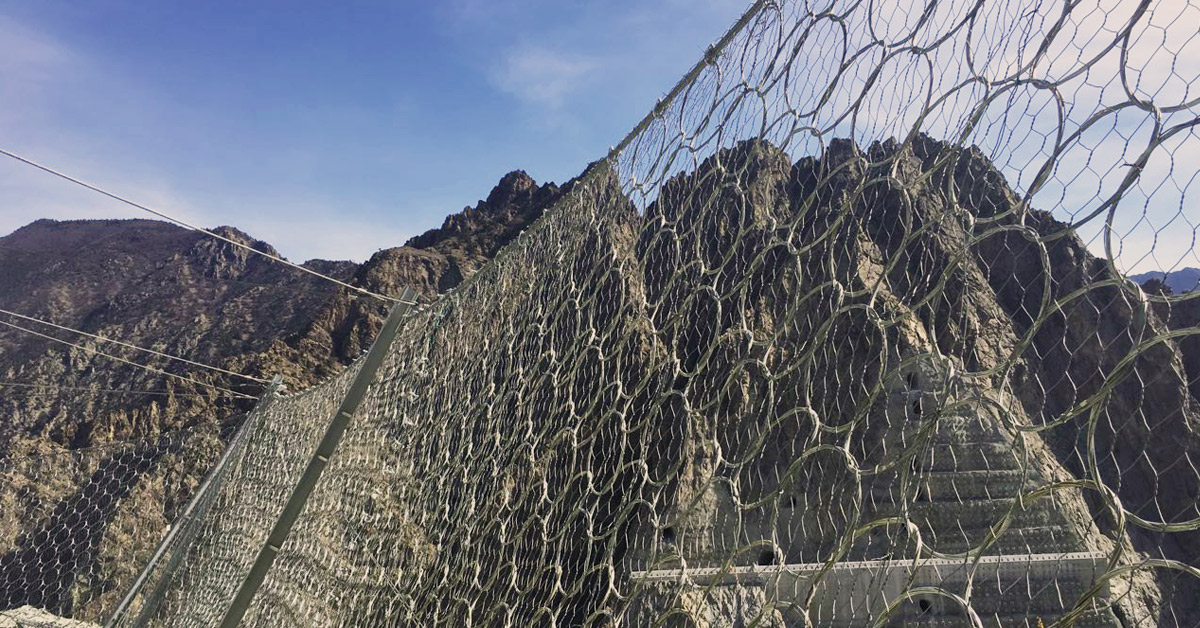
Yusufeli Barajı ve Hidro Elektrik Santrali Projesi’nin önemi hakkında bilgi verebilir misiniz?
Çoruh havzasında inşa edilen Yusufeli Barajı, gövde tipi olarak çift eğrilikli beton kemer kategorisinde 270 metre ile Türkiye’nin en yüksek, dünyanın da 3. yüksek barajı olacak. Barajın gövde yüksekliği temelden itibaren 270 metre olup, toplam depolama hacmi yaklaşık 2.2 milyar metreküp. Projede 3,5 milyon metreküp beton kullanılacak. Yıllık 1 milyar 888 kWh enerji üretilecek olan barajın ülke ekonomisine katkısı da yaklaşık 400 milyon TL olarak öngörülüyor.
Yusufeli Barajı Projesinin bir diğer önemi de tamamıyla yerli müteahhit ve mühendisler tarafından öz kaynaklarla yapılacak olmasıdır. Türkiye’nin ve Türk müteahhitlerin geldiği noktayı göstermesi açısından önemli bir projedir.
Yusufeli Barajı aynı zamanda farklı teknolojilerin ve çözümlerin uygulandığı bir proje olarak da Türkiye’de bir ilk diyebiliriz. Projenin zamanında tamamlanması için projelendirme aşamasında yer almayan ve proje ilerledikçe ortaya çıkan ihtiyaçlar doğrultusunda yeni çözümler geliştirmemiz ve uygulamamız gerekti. Bu anlamda da baraj projelerinde daha önce kullanılmamış yenilikler Yusufeli Barajında uygulanmış oldu.
Projede Maccaferri ile çalışmaya nasıl karar verildi?
Maccaferri ile daha önce Ankara-İstanbul ’Hızlı Tren Projesi’nde ve Bilecik yolunda çalışmalarımız oldu. Baraj projesi olarak da ilk defa bu projede çalışıyoruz. Daha önce yer aldığım baraj projelerindeki arazi koşulları ile buradaki koşullar çok farklı. Arazinin çok dik olması nedeniyle emniyetin ön planda olması gereken bir çalışma yapılması gerekiyor. Projenin hızlı ilerlemesi için işlerini düzgün, kaliteli ve zamanında yapan firmalar ile çalışmayı tercih ediyoruz. Limak Holding’in genel prensibi de bu yöndedir. İşin zamanında bitirilmesi oldukça önemli ve riske etmek istemediğimiz konular. Önemli olan işin zamanında, düzgün ve bizim istediğimiz kriterlerde yapılması. Daha sonradan her hangi bir problemle karşılaşmamak yada bir problem yaşandığı zaman anında çözüm önerileri sunulması, destek verilmesi bizim için son derece önemli. Ana kriterlerimiz ve prensiplerimiz bunlar. Dolayısıyla Maccaferri gibi firmalarla çalışmaktan memnunuz.
Projede kullanılan Maccaferri ürünleri nelerdir?
Kırma eleme tesislerinde uygulaması yapılan kaya bariyerlerimiz var, daha çok da arazide üst kotlarda. Moloz bariyer olarak 2.000 kj kapasiteli bariyer uygulaması yapılacak. Şev uzunluğu olarak yapılan kaya bariyeri toplam 760 metretül uzunluğunda. Projedeki çelik grid uygulamamız da yaklaşık 35 bin metrekare yapılacak. Çelik grid uygulamasının yaklaşık olarak 25 bin metrekarelik kısmı yapılmış durumda. Bu uygulamanın bir kısmı yüksek kapasiteli ağ dediğimiz mukavemetli çelik grid ürünleri. Bu uygulamalar yüzeysel döküntülerin kontrollü bir şekilde düşürülmesi amaçlanarak projelendirilmiştir. Kaya bariyerinde de 6 yüz metrelik bir alan uygulaması yapılmış durumda.
Maccaferri tarafından proje için özel olarak geliştirilmiş çözümler oldu mu?
Uygulamanın başında yapmaya başladığımız çelik grid uygulamasına, daha riskli olan bölgeleri emniyete almak açısından çelik grid uygulamasının yanında yüksek kapasiteli ağ dediğimiz ağlar (halka panel) kullanılmasına karar verildi. Aynı zamanda İSG ekibimiz ile birlikte proje süresince hangi uygulamanın uygun ve güvenli olduğu ile ilgili de görüşülüyor.
Tüm süreç boyunca Maccaferri ile olan diyaloglar nasıl ilerledi?
Referans olarak gösterir misiniz?
Maccaferri ile proje aşamasında, projenin işleyişi ve imalat süresinde çalışmaktan memnunuz. Kalite, güven, satış sonrası hizmet, verilen sözlerin yerine getirilmesi ve işin zamanında yapılması bizim için oldukça önemli ve bu anlamda da Maccaferri ile çalışmalarımızdan son derece memnunuz. Diğer projeler için de referans olarak göstereceğiz.
Taahhüdünüz altında yapım çalışmaları devam eden Yusufeli Barajı ve Hidro Elektrik Santrali Projesi ve yapım süreçleri hakkında bilgi verebilir misiniz?
Projeye fiili olarak Mayıs 2013’te başladık. Bitiş tarihi olan 29 Mayıs 2018’de suyun tutulacağı taahhüdünü verdik. Projeye ağırlıklı olarak yer altında yapılan çalışmalarla yani derivasyon tüneli kazı çalışmaları, giriş çıkış alanındaki kazı çalışmaları ve diğer ünitelere ulaşım tünelleri ile başlandı. 2014 Mayıs-Haziran aylarında ise açık gövde kazı çalışmaları başladı. 2015 yılının Eylül ayında kablo ve vinç sistemleri kurulunca kret altı kazılarına başlandı. Ana gövdenin kret kotu olan 715 kotu altı çalışmalarda ulaşımın zorluğundan dolayı kablolu vinçle veya 220 tonluk vinçlerle makineleri indirip kaldırmaya başladık. Projede kullanılmakta olan kablo vinç sistemlerinin kurulmasının amacı, zor şartlar altında hem kazıya hem de makine nakliyesine yardımcı olmak.
Şu ana kadar projenin finansal olarak % 66’sını bitirdik. 2016 Ağustos-Eylül ayları gibi de gövde beton imalatına başlamayı planlamaktayız. Santral binası içinde elektrik üreten toplam üç adet ünite mevcut. Bu tribünlerin kurulu güçleri ise 558MWh.
Projenin gerektirdiği yerlerde işi daha çok hızlandıracak çalışmalar ve çözümler üretiliyor. İlk olarak derivasyon tüneli çalışmalarına başlanırken enjeksiyon galerisini yaklaşım tüneli olarak kullanıp, giriş ve çıkış tarafına doğru kazıyı iki taraftan da tamamlayıp daha hızlı ilerledik. Sonuçta 2013 yılının Mayıs ayında başlanan çalışmalar 1 Nisan 2014’de suyun derivasyona çevrilmesi ile sonuçlandı. 11,30 metre beton iç çapı ve 901,60 metre uzunluğunda olan bir tünel kazısı bitirildi, beton imalatları yapıldı ve suyun derivasyona çevrilmesine hazır hale getirildi. Projenin işleyişinde yer alan kazı çalışmalarının daha randımanlı ve verimli yapılabilmesi için gereken sistemlere geçildi. Arazi üzerindeki açık kazılarda zeminin stabilitesinin sabitlenmesi, deprem, iklim şartları vb. gibi dış etkenlerden dolayı gövdeye zarar gelmemesi ve emniyetli bir çalışma alanı sağlanması için ankraj sistemleri yapıldı. Ayrıca aşağıya doğru inerken gövdedeki açık kazılarda kaya bariyeri ve tel kafesin haricinde zemini tutturmak için aktif ve pasif desteklemeler yapılıyor. 16 metreden başlayıp 60 metreye kadar çıkan aktif ankrajlarımız var. 60 metrelik delginin yapılması zor bir işlem olduğundan, bu işlemlerin nasıl hızlı bir şekilde yapılacağını tespit etmek için ekskavatör ataşmanı kullanıldı. Bu ataşman sayesinde 60 metrelik delgiler çok kısa sürede yapıldı ve kazı çalışmaları çabuk ilerledi. Gövdede yaklaşık 4,5 milyon metreküp kazı çalışması yapılacaktır. Yapılan çalışmalarda sol sahilde 550 kotlarına geldik yani temele kadar yaklaşık 105 metre kaldı. Sağ sahilde de 610 kotundayız, burada da temele 165 metre kaldı.
Projede kullandığımız kablolu vinç sistemi de her barajda olmayan ve özellikle beton kemer barajlarda daha çok dağın yapısına ve arazinin durumuna göre kullanılan bir sistemdir. Bu sistem sayesinde kazı çalışmalarımızı daha kolay devam ettiriyoruz. Gövde imalatında da aynı şekilde kablolu vinç sistemini kullanacağız. 3,5 milyon metreküp beton dediğimiz zaman bu betonun dökümü için büyük bir konkasör tesisi ve beton santrali gerekiyor. Kurulması planlanan beton santrali üretimi ise 360 metreküp/ saat. Gövde betonu imalatında, ayda ortalama 100 bin metreküp imalat yapmayı öngörüyoruz.
Projede kullanılan başka bir sistem de Raise Boring sistemi. Yer altı kazılarında, dikey şaft kazısı Raise Boring sistemi ile yapılmakta. Tünellerimizde dikey eksende iki tane şaftımız var. Biri su alma yapısında yaklaşık 64 metre olan kapak şaftı, bir diğeri de enerji tünelinin şaftı ki o da yaklaşık 140 metre. Yani 140 metre yukardan su aşağıya düşerek santrale gelecek, santralde tribünlerden geçerek elektrik üretilecek. Bu iki şaftın yapılmasında da Raise Boring sistemi kullanıldı. Raise Boring gibi sistemler işin önünü açan, daha çabuk ilerlememizi sağlayan ve işi emniyetli yapmamızı sağlayan sistemler.
Projede ne gibi sıkıntılar yaşadınız?
En büyük sıkıntı ulaşım sıkıntısı oldu. Açık kazılara başlamak için helezon tünellerle, önce bu alanlara ulaşmak ve makineleri oraya taşımamız gerekiyor. Bir diğer önemli konu da iş güvenliği. İşin emniyetli yapılması ve çalışanların güvenli çalışması bizim için son derece önemli. Aynı zamanda makinelerin de yüksek kotlarda güvenli çalışması, nakli, bakımı gibi sıkıntıları da düşünmemiz ve gerekli önlemleri almamız gerekir. Bunun için de kaya bariyeri, çelik grid gibi imalatlar gerekiyor. İş süresince de belli aralıklarla kontrollerimiz yapılıyor. Arada işin durdurulup yukarıda gerekli temizliklerin yapılması, gerekli emniyetlerin ve önlemlerin alınması gerekiyor. Projenin ilerleyişine ve sonradan oluşan koşullara göre moloz bariyer, yüksek kapasiteli ağ imalatları gibi ihtiyaçlar da oluşabiliyor. Şantiye alanı da dahil her yerde aynı emniyetleri alıyoruz. Şantiye tesislerinin arkasında, konkasör tesisinde de çelik grid uygulamalarımız yapıldı. Bunlar proje başlangıcında ön görülmeyen ancak daha sonra ihtiyaç doğrultusunda ve işin gerekliliğinden yapılmasına karar verilen uygulamalar. Çıktığımız noktalar mutlaka dağcılık faaliyetlerini gerektiren yüksek rakımlar. Sadece 860 kotu değil bizim daha yüksek kotları da, örneğin 900 kotlarında oluşacak sıkıntıları da öngörerek hareket etmemiz gerekiyor. Dolayısıyla proje de kendi içinde zamanla gelişiyor. İhaleye çıkıldığı zamanki kazı kotları ile şimdiki arasında aşağı yukarı 100 metre fark var. Kot farkını 100 metre aşağıya çekmek demek kazı miktarının düşürülmesi, püskürtme betonu ve pasif desteklemelerin yapılacağı yüzey alanların daraltılması ve projede işin önünün açılıp ekonomiye gidilmiş olması anlamına gelmekte. Bu uygulama yapılmasaydı henüz 715 kotuna ulaşmamış olurduk.
Projenin en zor kısmı başlangıç yani en tepeye çıktığımız kısımdı. Makinelerin en tepede durması, çalışması, ulaşımının problemli olması nedeni ile hep dikkat ve özen gerektiren çalışmalar yapılması gerekiyor. Aşağıya indikçe yavaş yavaş sistem de oturuyor ve yapılan her iş belli bir sisteme ve emniyete göre yapılıyor. Yerinde yapılan tüm çalışmalarda önceliğimiz güvenlik. Sahaya ilk çıkıldığında İSG departmanı alınması gereken önlemleri tespit ederek, gerekli çalışmaları yaparlar. Başlangıç kısmında yer alan boş zemin ve kayaların temizlenmesi ile buna rağmen daha yukardan düşebilecek kayaların oluşturacağı risklerin tespit edilmesi gerekiyor. Risklerin tespit edildikten sonra emniyete alınması, bariyerlerin yapılması, çelik grid ve yüksek kapasiteli ağ gibi imalatlar yapılıyor, sonra aşağıya doğru inmeye başlıyorsunuz. Bir aksilik olmazsa ağustos eylül aylarında temele inip gövde betonu imalatına başlamayı planlıyoruz.